Core Products & Services
Our products are systems that provide the ability to vacuum convey conditioned powder from various powder sources, mix powder with the liquid media on a single pass, batch recycle, batch and pump or continuous steady-state basis via Vacucam® Ejector Mixer (EJM) and discharge the mixture forward into an existing tank.
Core Products
One beverage process system can be configured for up to four options.
VACUCAM® Dynamic Beverage Batching Station (DBBS)
One Beverage Process System – many process applications for all powder handling and mixing. System can be configured for one, two, three, or four process options to handle basic Beverage production from small to large volume dry ingredient additions. Mix tanks range from 250-500+ gallon capacity, depending upon best suited process option.
This system provides ability to vacuum convey conditioned powder from various powder sources, mix powder with the liquid media on a single pass, batch recycle, batch and pump or continuous steady-state basis via Vacucam® Ejector Mixer (EJM) and discharge the mixture forward into an existing tank. Liquid media is metered into the supply line to the EJM supply pump. This mixer supply pump provides liquid flow and pressure to EJM to generate a powerful vacuum used to inhale dry ingredients and rapidly mix and dissolve / disperse them into liquid(s). Mixture is continuously batched in a slurry / mix tank and transfers forward to a blend tank. Vacucam® DBBS Dynamic Beverage Batching System includes both bulk bag unloading capability as well as dry minor’s funnels and small tank for floor level addition of minor liquid ingredients from totes, barrels, or bins.
Batch accuracy is maintained / confirmed thru use of loss in weight on dry hoppers, liquid flow meters on incoming / recycled liquid and density meter on outbound flow where density and concertation can be gleaned and uses in totalization scheme in batch recipes when using full bulk dry side (silos).
Single Pass Process w/ Transfer to Blend Tanks:
Process allows for high usage dry ingredients being conveyed and mixed with process water as it is pumped directly to selected blend tank(s). Dry ingredients can be fed from bulk bags or paper bags. Used for optimum dissolution of thickeners, gums, dairy protein powders, and sensitive ingredients, typically lower solids (<20-30%).
Batch Recycle Process – Batch & Pump-away of Dry Ingredients
Batch Recycle addresses requirements of typical beverage processes to efficiently convey, mix and dissolve / disperse dry ingredients before transfer to blend tank(s). Used for handling most medium volume ingredients, including those with higher solids. Can be configured as batch recycle to/from existing large blend tanks or as batch recycle from SBS skid mounted blend tank then entire concentrate pumped forward (MOT (mixer on a tank, batch and pump))
Dynamic Continuous Steady State Process (DCSS)
DCSS process allows for high usage dry ingredients being conveyed and mixed to a “set-point” solids level while continuously being delivered to blend tank(s). High usage dry ingredients, such as sucrose can be continuously conveyed, totally mixed and delivered to blend tank(s) without multiple batch transfers. Density meter measures and totalizes dry product mass for each batch providing weighment accuracy to +/- 1% when coming from total bulk (silos, bulk trucks, railcars).
Liquid Concentrate Transfer
Integral liquid funnel allows liquid concentrates to be dumped at floor level and transferred to blend tank(s) via DBBS transfer pump
VACUCAM® Dynamic Continuous Steady-State (DCSS)
System provides the ability to vacuum convey conditioned powder from various powder sources, mix powder with liquid media in an on-demand basis via Vacucam® Ejector Mixer (EJM) and discharge mixture into an existing batch tank. Liquid media is metered into supply line to EJM supply pump or recycled from mix tank.
Dry Side: Powders are manually or automatically weighed from various packaging formats, including bulk bags and full bulk such as silos, day bins, bulk truck trailers Each modular-designed skid can sequentially inhale dry products from various sources for fast efficient multi ingredient formulations.
Wet Side: Liquid media is meter into supply line remote supply pump. EJM supply pump provides liquid flow and pressure to EJM to generate vacuum to inhale dry ingredients and rapidly mix and dissolve / disperse them into liquid(S). Mixture is batched in a mix tank and then transfer pump transfers mix to a batch tank. Density meter measures and totalizes dry product mass for each batch providing weighment accuracy to +/- 1% when coming from total bulk (silos, bulk trucks, railcars).
VACUCAM® Inline Batching Process
System provides ability to vacuum convey conditioned powder from various powder sources, mix powder with liquid media on a Single Pass or Batch Recycle basis via Vacucam® Ejector Mixer (EJM). After leaving the mixer discharge tube, slurry is de-aerated by tangentially entering a de-aeration tank where cyclone action spreads liquid into a thin film on tank wall, forcing entrained gases out and up tank vent. A baffle directs flow to take-away pump where it is continuously pumped forward to blend tank(s).
Dry Side: Powders are manually or automatically weighed from various packaging formats, including pre-weighed paper bags, loss in weigh paper bags and / or bulk bags and full bulk such as silos, day bins, bulk truck trailers. Each modular-designed skid can sequentially inhale dry products from various sources for fast efficient multi ingredient formulations.
Wet Side: Liquid media is metered into supply line to EJM via a remote supply pump (Single Pass) or recycled from batch tank (Batch Recycle). Mixer supply pump provides liquid flow and pressure to EJM to generate vacuum to inhale dry ingredients and rapidly mix and dissolve / disperse them into liquid(s).
VACUCAM® Mixer on Tank (MOT) Batching Process
This system provides the ability to vacuum convey conditioned powder from various powder sources, mix the powder with the liquid media on a Single Pass or Batch Recycle basis via the Vacucam® Ejector Mixer (EJM). After leaving the Mixer discharge tube, slurry is de-aerated by tangentially entering the mix tank where cyclone action spreads liquid into a thin film on tank wall, forcing entrained gases out and up tank vent. A baffle directs flow to take-away pump where it pumped to the batch tank.
Dry Side: Powders are manually or automatically weighed from various packaging formats, including pre-weighed paper bags, loss in weigh paper bags and / or bulk bags and full bulk such as silos, day bins, bulk truck trailers. Each modular-designed skid can sequentially inhale dry products from various sources for fast efficient multi ingredient formulations.
Wet Side: Liquid media is metered into supply line to the EJM via a remote supply pump (Single Pass) or recycled from batch tank (Batch Recycle). Mixer supply pump provides liquid flow and pressure to EJM to generate the vacuum to inhale dry ingredients and rapidly mix and dissolve / disperse them into the liquid(s).
VACUCAM® Mixer on Stand (MOS) Batching Process
System provides ability to vacuum convey conditioned powder from a powder funnel, mix powder with liquid media on a Single Pass basis via Vacucam® Ejector Mixer (EJM), and discharge mixture into a batch tank.
Dry Side: Powders are manually weighed and dumped into hopper.
Wet Side: Liquid Media is metered into supply line to EJM supply pump, which provides liquid flow and pressure to EJM to generate vacuum to inhale dry ingredients and rapidly mix and dissolve / disperse them into liquid(s).
VACUCAM® Mixer on Stand (MOS) Batching Process for Paint Thickeners
System provides ability to vacuum convey conditioned powder from a powder funnel, mix powder with liquid media on a Single Pass basis via Vacucam® Ejector Mixer (EJM), and discharge mixture into a batch tank.
Dry Side: Powders are manually weighed and dumped into hopper.
Wet Side: Liquid Media is metered into supply line to EJM supply pump, which provides liquid flow and pressure to EJM to generate vacuum to inhale dry ingredients and rapidly mix and dissolve / disperse them into liquid(s). A flowmeter and shut-off valve can be added to better measure and control amount of liquid media.
Customized Process Xstreamlining Solutions
Semi-Bulk Systems, Inc. is considered a true partner in developing specific processes customized to maximize competitive and profitability positions. Our patented processes; our modular skidded approach to provide a Total Solution for both dry side and dry/liquid mixing; and our focus on providing major benefits vs. traditional processes have revolutionized the markets we serve including Beverage, Dairy, Food, Health & Beauty, Paint & Coatings, Paper, Power Generation, Chemical Manufacturing and more!
Do you need process improvement to increase efficiency, lower process costs, save labor costs, and increase your bottom line? Our Process XStreamlingsm solutions can help you accomplish these goals.
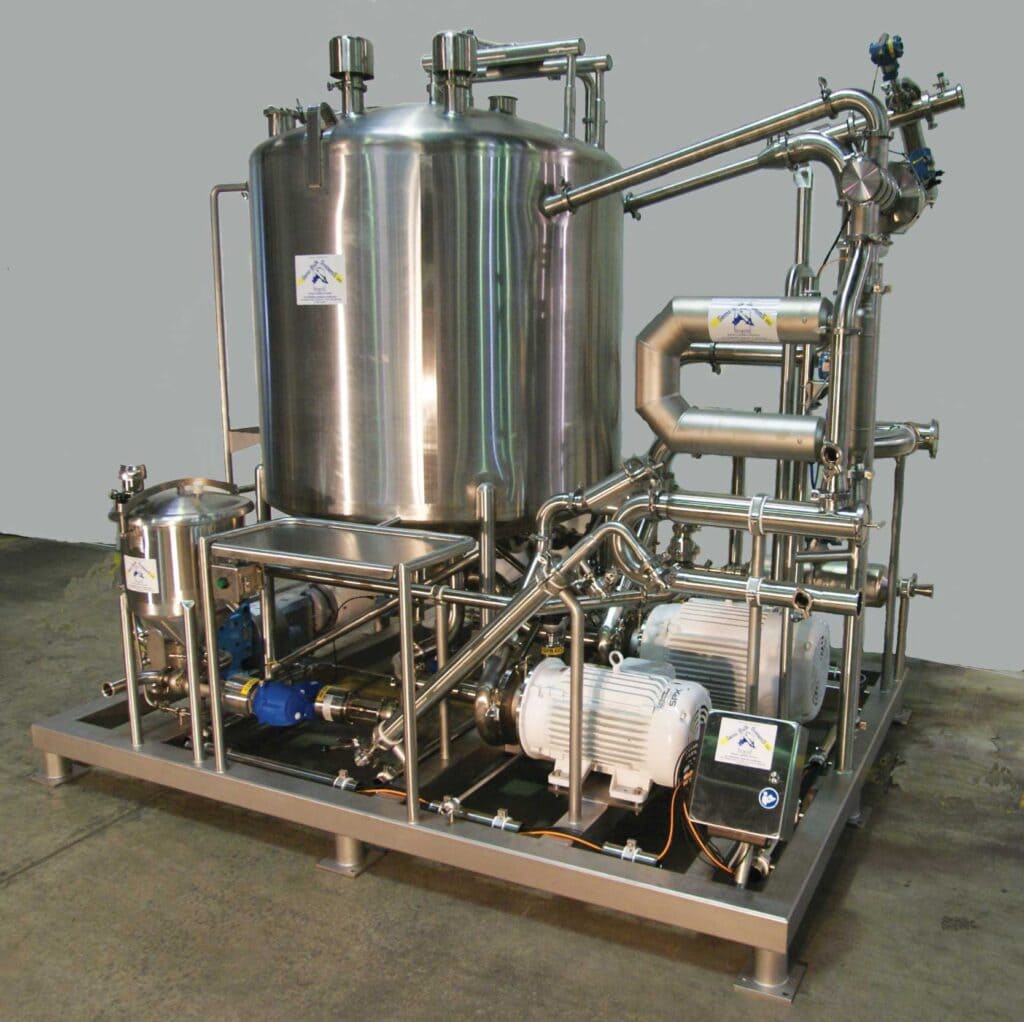