How a top food manufacturer achieved a higher production efficiency for starch slurries.
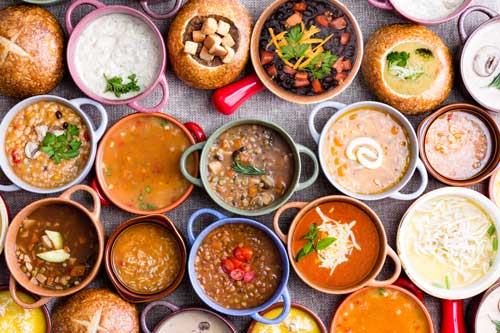
Opportunity
Our Approach
Semi-Bulk Systems designed a Process XStreamlining Solution that utilized the Vacucam® Continuous Steady State technology to improve slurry process efficiency. The system provides the features needed:
- Incorporates the integration of bulk truck unload process (500 #/min) to Vacucam® Continuous Steady State Slurry Process for Corn and Tapioca starches.
- Integration of the Vacucam® dynamic dispersion technology to deliver a predetermined solids level (35-40%), fully hydrated and ready to use on a continuous basis.
- Dry delivery portion designed for effective dust containment.
The Results
We delivered Our Performance Guarantee that:
- Capacity: significant batch cycle reductions when compared to traditional batching processes.
- Operating costs: dramatic reductions in both labor and energy costs.
- Operating costs: lower maintenance, unplanned downtime with no moving parts
- Quality: batch-to-batch consistency producing no fisheyes or agglomerates
To see if Semi-Bulk’s state-of-the-art VACUCAM mixing technology and pet care production solutions can improve your production efficiency, contact us or call 800-732-8769.